How to Solve the Problem of Surface Wear on Track Shoes?
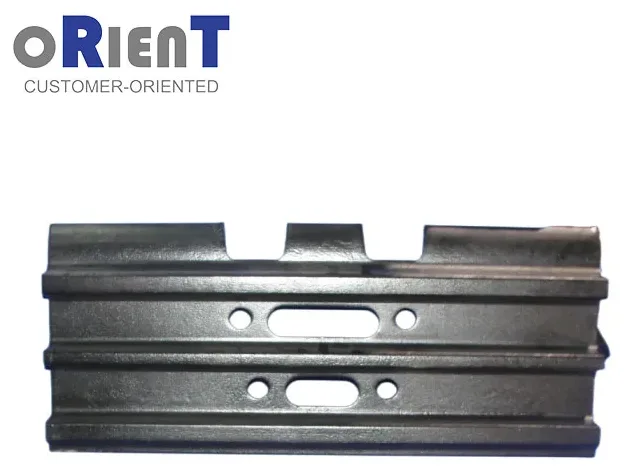
Uniform Grouser Wear on Track Shoes
When wear is quite even over the entire surface of the grousers, it must be considered as normal.
- Causes
Sliding contact with underfoot material.
- Accelerators
Any condition which increases the contact force or the abrasion of the grousers with the ground, will contribute to grouser wear.
These conditions include: machine weight, horsepower, speed, impact, soil abrasiveness, terrain, and all the operating variables that cause unproductive slippage, turning or sliding.
- Effects
Loss of traction, bending strength and regrouserability when wear limits are exceeded.
- Remedies
Reduce or eliminate controllable variables.
Use extreme service shoes if the single grouser shoe has to be replaced before pin and bushing turn.
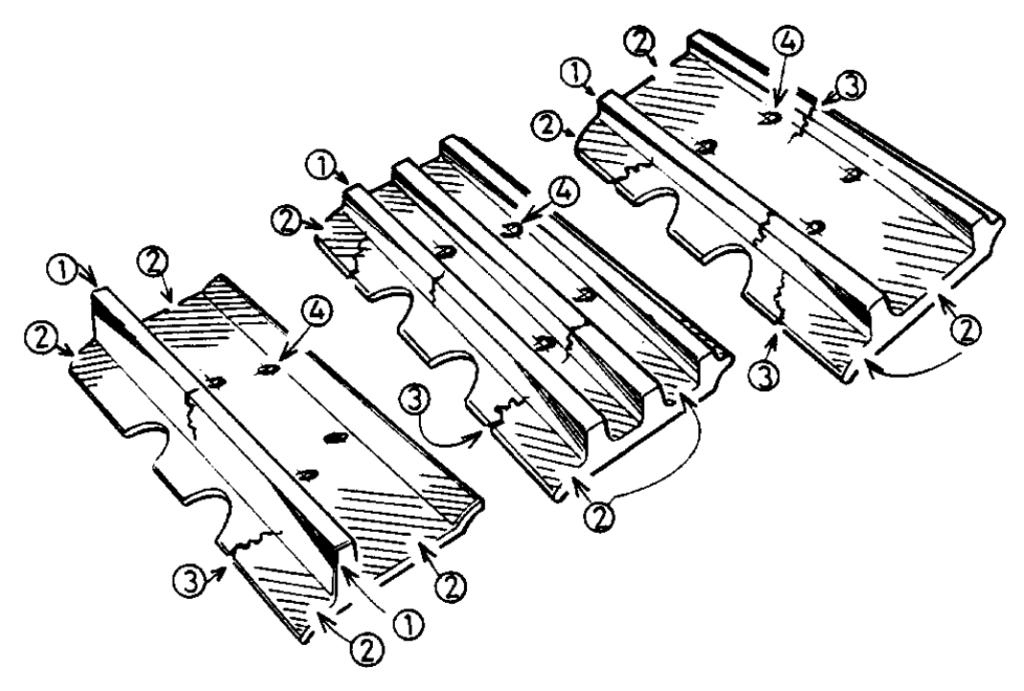
① Grouser Tip Corner Wear on Track Shoes
Grouser corners display higher wear levels than the centres.
- Causes
Same as “normal” wear, but different underfoot conditions and operating accelerators are predominant.
- Accelerators
High impact conditions can be very detrimental for grouser corners. Especially in combination with excessively wide shoes and frequent turning operations.
- Effects
Reduced wear life and traction.
- Remedies
Adopt the proper shoe width and eliminate or reduce controllable variables.
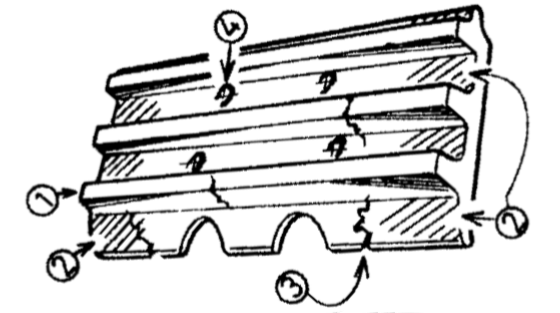
② Shoe Plate Deformation and Wear
Bending and wear of the shoe plate, including leading and trailing edges..
- Causes
The general causes are the same as for “normal” wear.
- Accelerators
Progressive wear of the shoe in heavy duty applications.
Abrasive soil and small rocks entering in the overlapping area between leading and trailing edges will result in faster wear of these parts of the shoe.
The leading-trailing edges are also affected in the event of internal wear of the joints.
- Effects
Loss of traction and regrouserability.
Risk of breakage.
- Remedies
Same as “Uniform Grouser Wear”.
Adopt the proper shoe width and eliminate or reduce controllable variables.
Install a sealed and lubricated track chain if wear of leading and trailing edges is critical.
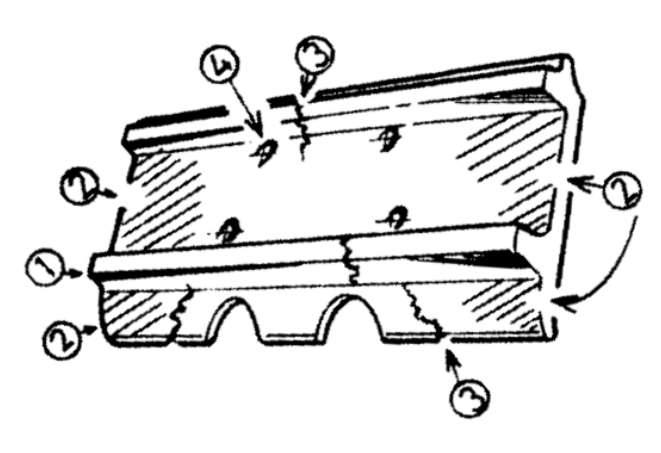
③ Shoe Cracking and Breaking
- Causes
When stresses due to the load on the shoes exceed the mechanical resistance of the material cracks and breakages may occur.
- Accelerators
Apart from typical accelerators, shoe width is the most important factor in determining the resistance of the shoe to the applied forces.
- Effects
Reduced exploitation of shoe wear life.
- Remedies
As usual, the choice of the narrowest shoes able to provide adequate flotation is the best solution. If available, extreme service shoes should be used in the case of heavy duty applications.
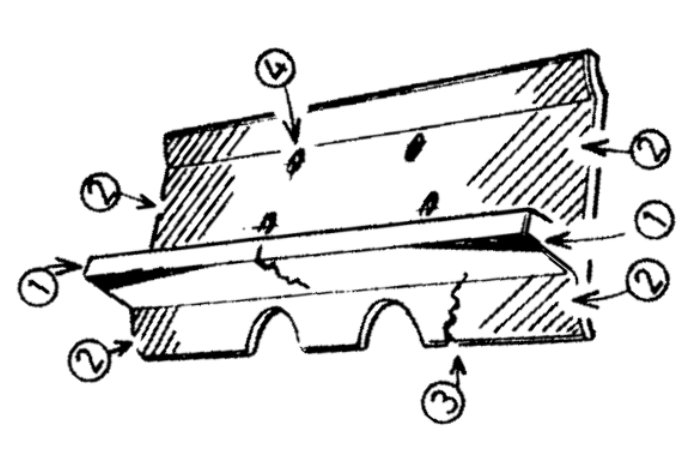
④ Bolt Hole Deformation
Enlargement or ovalization of the bolt holes.
- Causes
Loosening of the mounting bolts due to:
- incorrect tightening torque at the time of installation;
- lack of cleanliness between the link and the shoe mounting surfaces:
- lack of scheduled maintenance:
- elongation of the bolt due to excessive loads that force the joint up to the yield point.
- High turning resistance in rocky conditions.
- Accelerators
Excessively wide shoes, bolts overtorqued at installation.
- Effects
Loss of unused wear life, regrouserability and possible damage to link bolt holes.
- Remedies
Choose the narrowest shoe able to ensure adequate flotation.
Always use the recommended bolt torque and follow the tightening instructions as described in the “Service and Maintenance” section of this handbook.
If possible, clip ends of grouser to reduce turning resistance of wide shoes.
When convenient in terms of productivity, adopt multi grouser shoes in order to reduce turning resistance.
Remove all paint, dust and rust from mating surfaces at the time of installation.
Use new hardware when installing new shoes.