Tread Wear on Track Roller
Tread Wear on Track Roller is the normal wear pattern
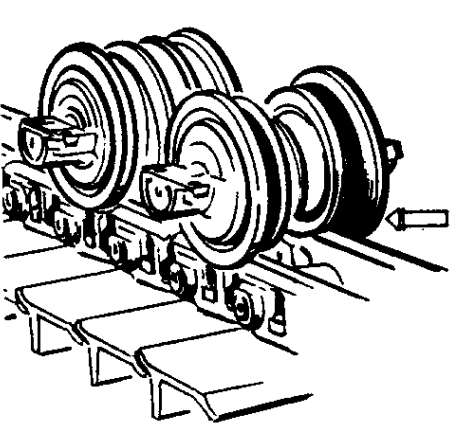
Causes
Rolling contact with the abrasive particles of the soil between the roller tread and the link rail.
Sideways sliding contact between tread and rail.
Accelerators
Machine weight, horsepower, speed, impact abrasiveness and packing.
Turning increases sideways sliding contact.
Excessively wide shoes and track snakiness tend to generate rounded wear patterns.
Effects
Interference between roller flanges and link pin bosses, when both the roller and the track chain have reached their service limits.
Higher angular velocity in order to obtain a given speed.
Remedies
Eliminate or reduce controllable accelerators as far as possible, particularly unproductive turns and excessively wide shoes.
If economically viable, when different wear is displayed between the rollers they can be swapped in order to balance final wear lives.
Offset Tread Wear and/or Flange Side Wear on Track Roller
The wear pattern on the treads is shifted from the centre axis of the roller.
Inner and/ or outer sides facing tread wear.
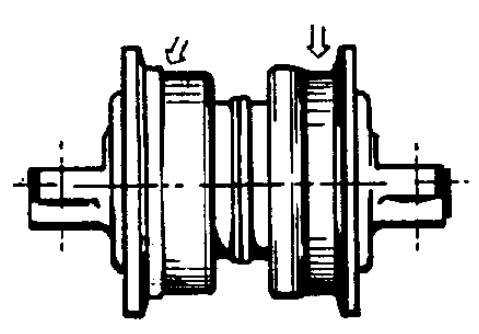
Causes
Misalignment of the roller frame.
Rolling and sliding contact with the sides of the link rail.
Inadequate track guidance.
Eccentric loading point of machine due to application (e.g.: plough work, use of the side blade only, etc.).
Use of improper track chains or rollers.
Accelerators
Same as “Roller Tread Wear”
In addition, also the following accelerators must be considered: predominant sidehill operations, snaky track chains, excessively wide shoes, uneven terrain.
Effects
Reduced wear life of rollers and track links.
Tendency of machine to drift laterally with respect to a linear trajectory.
Increased risk of track chain derailing or jumping.
Remedies
Same as “Roller Tread Wear”.
If possible, install double flange rollers.
When allowed by the other variables, replace or install final drive guiding guards.
Correct alignment problems.
Install on the machine only the components that are designed for it, or those that are considered fully interchangeable in our spare parts catalogue.
Flange Top Wear
Wear of flange tops.
Causes
Rolling and sliding contact with the pin boss due to loss of clearance.
Accelerators
Same as “Roller Tread Wear”.
Effects
Damage of the link pin boss could result in a loss of pin retention.
Remedies
Same as “Roller Tread Wear”.
Avoid exceeding the wear limit of undercarriage components.
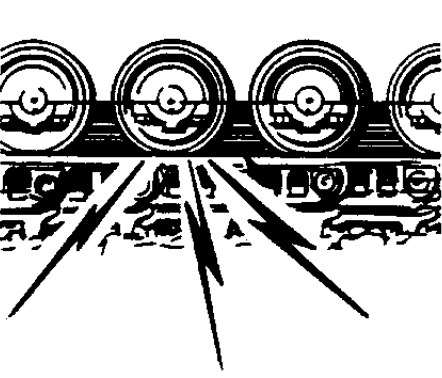
Flat Spots on Track Roller
Flat areas on the roller tread.
Causes
- Sliding wear due to the following:
- packing situations which prevent the roller from rotating;
- frozen soil or water around the roller sitting overnight;
- internal seizing or gutting.
Effects
Increased wear of the track chain links
Vibration at high speed travel.
Interference between roller flanges and link pin boss.
Remedies
Remove rock guards, if possible.
Keep the undercarriage as clean as possible.
In wintertime, clean accumulations of dirt from undercarriage without using water or fluid subject to the risk of freezing
Maintain the proper track tension.