Quality Issues and Observations
When conducting a borehole inspection, the probe may encounter blockages at certain depths, preventing a smooth inspection of the hole’s bottom. Additionally, the diameter of the borehole might be smaller than the design specifications, or it may decrease progressively from a certain depth.
Causes
- Presence of Weak Geological Layers: Weak layers in the geological structure can be compressed into the borehole due to earth pressure, resulting in a shrinkage hole.
- Expansion of Plastic Soil: In geological structures, when plastic soil comes into contact with water, it can expand and create shrinkage holes.
- Drill Wear: If the drill wears out too quickly and is not repaired or welded in a timely manner, shrinkage holes may form.
Preventive Measures
- Monitor Geological Data: Pay close attention to geological drilling data and soil quality changes. If weak layers or plastic soils are identified, ensure frequent cleaning of the borehole.
- Regular Drill Inspections: Frequently check the drill’s condition and perform timely repairs or welding when wear is detected. After repairing or welding, ream the drill to ensure it meets the design pile diameter.
Treatment Measures
If shrinkage holes occur, use the drill to repeatedly clean the borehole until the diameter meets the design specifications.
For any inquiries about Rotary Drilling Rig Undercarriage Parts, please contact us freely.
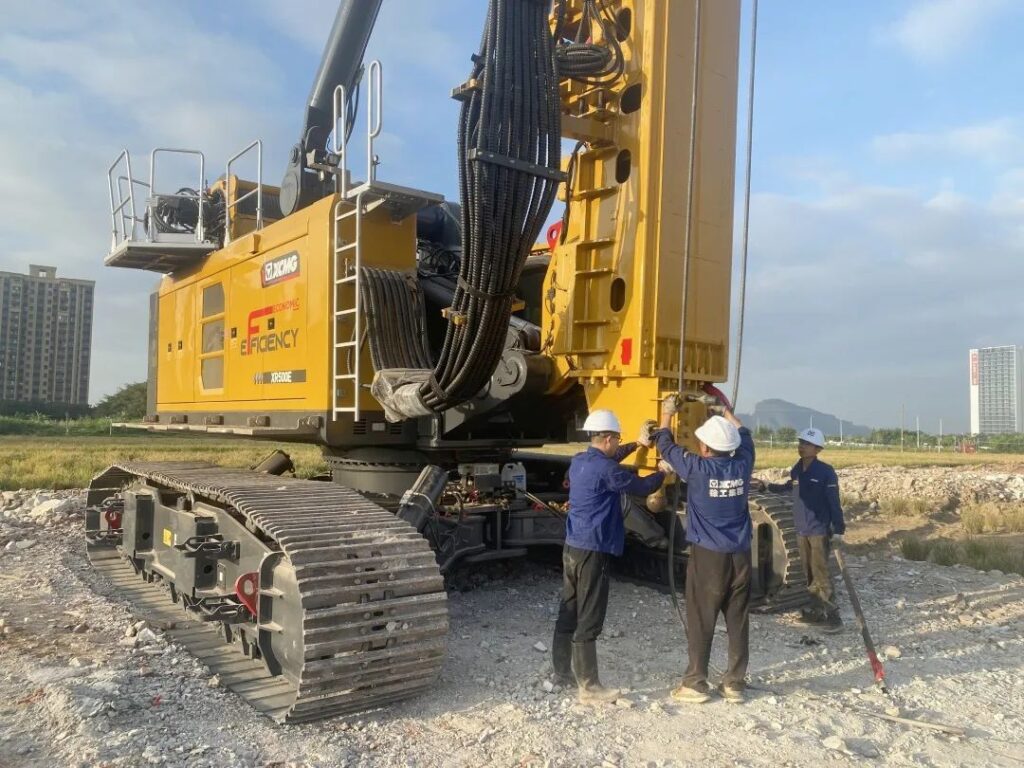