Drilling is a fundamental operation across various industries, but it can present several challenges that may lead to defects and increased costs. This article identifies the most frequent drilling problems, such as drill deviation, overheating, breakage, burr formation, and rapid wear, and provides practical solutions to mitigate these issues. Understanding these problems is crucial for improving efficiency and ensuring high-quality results in drilling tasks.
One prevalent issue is drill deviation, which occurs when the drill bit strays from its intended path. This can be caused by factors like a dull drill bit or improper pressure application. To address this, it is essential to use a sharp drill bit and mark the drilling point with a centering tool. Additionally, securing the workpiece and maintaining appropriate rotational speed can help prevent deviation. Another common problem is overheating the drill bit, particularly when drilling hard materials. This can be mitigated by using lubricants to reduce friction and selecting the correct rotational speed to avoid excessive heat buildup.
Drill bit breakage is another significant concern, often resulting from excessive pressure or poor-quality bits. To prevent this, using high-quality drill bits and applying moderate pressure is recommended. Burr formation, which leads to rough finishes, can be minimized by using well-sharpened bits and appropriate speeds. Lastly, rapid wear of drill bits can be addressed by selecting durable materials and maintaining proper drilling techniques. By implementing these solutions, one can enhance drilling performance and reduce operational costs.
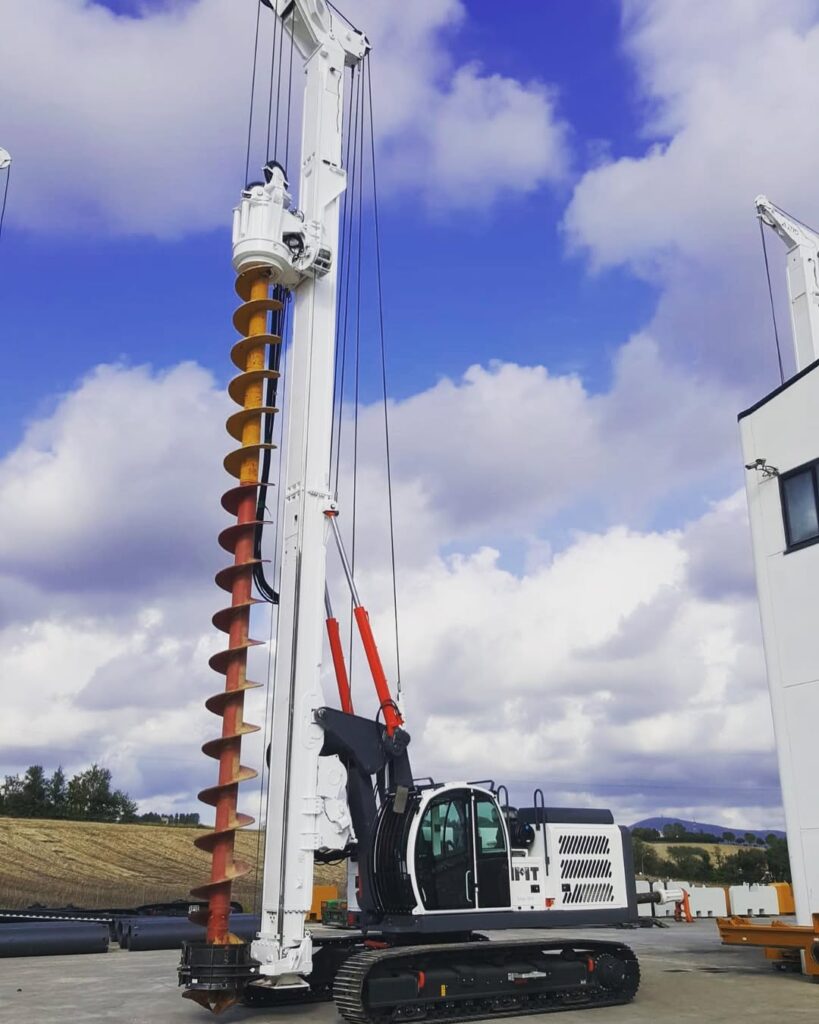
Drilling Challenges and Solutions
Drilling is a fundamental operation in various industries, but it comes with its own set of challenges that can affect the quality and efficiency of the work. Common issues include bit deflection, overheating, and rapid wear, which can lead to irregular holes and compromised assembly quality.
To mitigate these problems, it is essential to adhere to manufacturer guidelines regarding rotational speed and pressure, as well as to regularly sharpen drill bits and use appropriate lubricants. For abrasive materials, using coated drill bits can significantly enhance tool longevity.
Another prevalent issue is chip jamming, particularly when working with metals or plastics. Accumulated chips can block the drill bit, increasing friction and heat, which may damage the tool and affect the drilling quality. To prevent this, selecting drill bits with wide flutes and utilizing lubricants can facilitate chip evacuation. Regularly interrupt the drilling process to clear chips, and employ twist or double spiral bits. This can further reduce the risk of jamming.
Drill bit slippage and the creation of chips and cracks are additional concerns, especially when drilling brittle materials. Slippage can lead to misaligned holes, while chips and cracks can cause irreparable damage. To combat slippage, marking the drilling point with a punch and using specialized drill bits can enhance accuracy.
For brittle materials, using diamond or carbide-tipped bits, along with techniques like applying tape and using coolants, can minimize damage. Addressing excessive vibration through proper workpiece securing and maintaining consistent pressure is also crucial for achieving high-quality results in drilling operations.
For More Inquiry:
If you have any inquiries regarding our Drilling Rig Undercarriage Parts. Such as track shoes, track chain assembly, track roller, carrier roller, sprocket, or idler. Please do not hesitate to contact us.
Thank you for choosing us for your drilling rig spare parts needs. We are dedicated to providing high-quality products that keep your equipment running efficiently.