Mastering these four drilling rig construction techniques will increase the construction efficiency by 37%.
Drilling rig is a construction machinery suitable for drilling operations in building foundation engineering. It is widely used in municipal construction, highway bridges, high-rise buildings and other foundation construction projects. With different drilling tools, it is suitable for dry (short spiral), wet (rotary bucket) and rock formation (rock core drill) drilling operations. Rotary drilling rig has high installed power, high output torque, large axial pressure, and flexible mobility, high construction efficiency and multifunctional features.
The four major construction techniques are divided into: dry drilling process, mud static pressure process, casing process, and concrete wall making process.
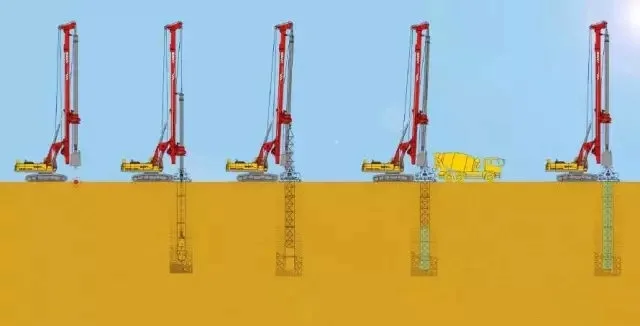
Dry Drilling Process
Characteristics of Dry Drilling Process
- Due to the strong and dense geological conditions, there is no need for other auxiliary drilling materials or equipment during drilling, and drilling can be done directly. The dry drilling process is the simplest technique in rotary excavation construction. Its characteristics are: simple process and low construction cost.
- The dry drilling process is suitable for hard plastic and sturdy geology. Before adopting the dry drilling process, it is necessary to grasp the conditions of the rock, soil, and groundwater, with the premise of not collapsing the hole.
Advantages and Disadvantages of Dry Drilling
- Disadvantages of dry drilling: Although there is no need to worry about hole collapse. However, due to the loss of lubrication, softening, cooling, and buffering from water and mud, the drilling resistance in certain formations increases. Especially for dense dry soil and coarse sand layers, it is particularly noticeable. Difficulty in slag pouring occurs, exacerbating drilling tooth loss and drilling rod vibration.
- Advantages of dry drilling: In addition to simple process and low construction cost. In specific geological conditions, due to the softening of mudstone when encountering water, the mud lubricates, resulting in slipping, tooth clogging, and lake bottom phenomena. Dry drilling can eliminate the above phenomena and improve the efficiency of shear crushing.
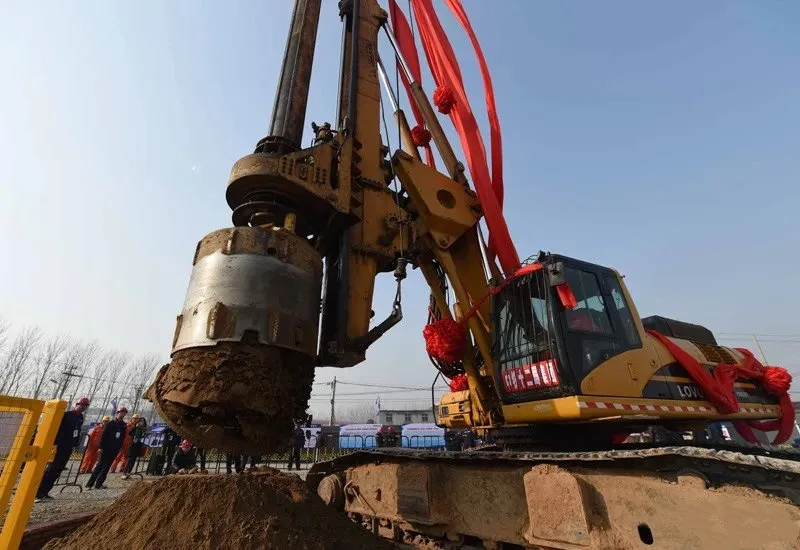
Mud Static Pressure Process
The Effect
Mud pressure supports the hole wall to prevent construction quality issues and accidents such as shrinkage, collapse, and buried drilling.
Three Indicators
- Mud pressure
- Mud wall protection
- Sand content
- Mud three piece set: mud density meter, mud viscosity meter, and sand content tester.
Other Effects
Mud specific gravity, viscosity, and sand content are important parameters in the action of mud, which ensure the quality of drilling and the safety of equipment and personnel. But in addition to support and wall protection, mud also has multiple other functions, playing different roles in different geological and groundwater conditions, including suspension, lubrication, cooling, shock absorption, buoyancy, and softening.
Mixing Ratio
Mud mix ratio: using bentonite as the slurry and wall protection process, the raw materials are water, bentonite, cellulose, and caustic soda. The mix ratio is 100:8:0.05~0.1:0.1~0.5.
Different Types of Mud Applications
Due to the diversity of geological types, variations in layer thickness and burial depth. And variations in groundwater levels, different geology and groundwater require different types of mud.

Casing process
Protecting Tube
- The role of casing is to protect the safety of pile holes, equipment, and personnel. Determine the length of the casing based on the rock, soil, and groundwater conditions. The length of the casing is generally between 2M and 4M. The diameter of the casing is usually greater than the pile diameter by 200MM;
- Lower casing method: reamer, drill bucket, special tooling, vibration hammer;
- Control requirements: Verticality and center deviation of buried casing.
Casing Pipe
The casing driver, pipe kneader or rotary drilling rig, as well as the vibration hammer burying the casing and the rotary drilling bucket following the pipe drilling inside the casing. The casing process can replace the mud wall static pressure process. Suitable for biting piles, inclined piles, unstable strata and outdoor construction, limited resources (without water and electricity), urban environmental protection construction, etc.
The function of the casing pipe
Support the hole wall and prevent collapse. The length of the casing is forcibly guided to prevent deviation from the hole. Sealing of casing to protect groundwater.

The structure of the casing pipe
① Drive plate: The drive plate is connected to the bottom of the power head drive sleeve through bolts, achieving structural transition. The function is to transmit torque and apply pressure.
② Connection plate: The connection plate is connected to the drive plate through a pin shaft. And reserve the connecting pin shaft with the casing driver.
③ Sleeve driver: The upper part of the casing driver is connected to the connecting plate through a pin shaft, and the lower part is connected to the sleeve. The diameter of the casing driver must match the diameter of the casing. The lower part of the casing driver has positioning grooves and stops for easy docking with the casing. The function of the casing driver is to transfer torque and pressure to the sleeve and boots.
④ Sleeve: The upper end of the sleeve can connected to the casing driver or sleeve through a pin shaft. The lower end of the casing can be connected to the casing or boot.
⑤ Connection pin: The sleeve fixes with a conical ring and a threaded ring. The docking and positioning of the sleeve are completed, and the sealing ring is installed on the support ring, twisted into a threaded ring and a tapered ring to achieve connection.
⑥ Boot: There is front end of the boot embeds with alloy drill teeth. By rotating and axial pressure, cutting various formations and rocks, reducing the resistance of buried casing, and improving the drilling ability of casing.
Running casing method: casing driver, pipe rolling machine, full rotation drilling rig
Applicable working conditions: urban construction, field construction
Applicable geology: silt layer, loose formation, large particle size solitary stones, unfilled karst caves, special foundations (interlocking piles, inclined piles)

Concrete wall making process
The concrete wall construction process of rotary drilling rig is not a formal rotary drilling process. This passive safety process lags behind the active safety of mud static pressure and casing technology, and has certain operational risks.
The Effect
Usually used for construction in plateaus, mountainous areas, backfill soil, and karst caves. Due to insufficient or no groundwater, or a lack of water resources. When using dry drilling technology for construction, there may be deviation and local collapse in the hole. Fill the hole with C15 concrete and the abnormal parts inside the hole. After the concrete reaches its initial setting strength, use a toothed drum drill to take the core and drill.
Backfilling concrete into the deviated hole can repair the deviated hole, and filling concrete into the local collapsed hole position can create a protective wall layer locally. Backfill the hollow karst cave with concrete, fill the karst cave and drill it into the guide to prevent jamming and deviation of the hole.
Application of concrete wall construction
- Karst cave geology
- Offset hole
- Local collapse hole
Precautions for concrete wall construction
- Lagging: Concrete retaining walls have certain advantages in treating karst caves and deviated pores. However, when dealing with local collapse holes, due to lag issues, if the drilling bucket collapses at the bottom of the hole, it is likely to cause buried drilling. Therefore, when adopting concrete wall protection, it is necessary to comprehensively understand the geological and borehole conditions before adopting this process.
- Construction efficiency: Using concrete walls requires time to reach the initial setting state. Therefore, it causes intermittent construction of single holes, reducing construction efficiency.
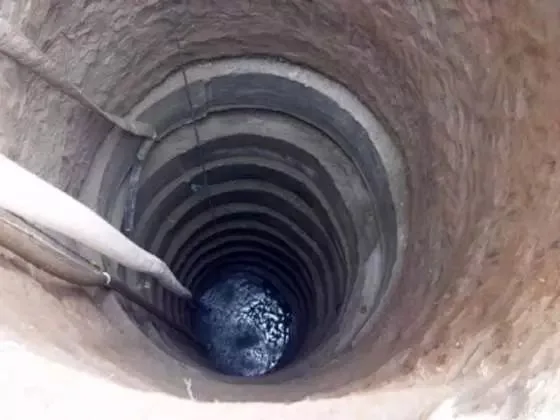