Track rollers are usually made up of several parts: wheel body, pins, and other components. The pins and wheel body of the track roller usually have their own process flow during the manufacturing process. The wheel body is the main part of the track roller, which is used to bear weight generate inertia force, and play a role in balancing vibration. The pin is the shaft connecting the wheel body and the mechanical system, supporting the rotation of the wheel body and transmitting inertia force to the system.
1. Pin
The roller pin of the rotary drilling rig is an important component of the rotary drilling rig, used to connect the roller and the main structure of the rotary drilling rig. The main function of the roller pin is to support the roller and transfer weight, helping to balance the center of gravity and stability of the rotary drilling rig during construction. The roller pin process includes the following steps.
Cutting:
The raw material is 40CrMo/42CrMo, and blanks that meet the size requirements are cut from the raw material during processing.
Rough turning:
The blank obtained by cutting is rough-processed to form a rough shape, leaving enough margin for subsequent processing.
Heat treatment (surface tempering):
The shaft is heat treated after rough machining, usually surface tempering treatment, to improve the hardness and wear resistance of the shaft.
Surface tempering is a heat treatment process that forms a hard and wear-resistant surface layer on the pin surface while maintaining the toughness and strength of the pin interior. This process usually includes two steps: quenching and tempering:
Quenching: The pin is first heated to above the critical temperature and then rapidly cooled to form a martensitic structure on the pin surface, thereby improving hardness and wear resistance.
Tempering: Then, the quenched pin is tempered, and the martensite is transformed into a more stable martensite + residual austenite structure by heating and keeping warm for a certain period of time, so as to improve the toughness of the pin.
It can improve the surface properties of the pin while maintaining the toughness of the core part, thereby extending the service life of the component and improving its wear resistance.
Finishing:
Heat-treated shafts are finely machined for greater precision and smoothness.
Drilling:
Drill holes on the shaft to install other components or connect accessories.
Surface grinding:
Use equipment such as an outer edge grinder to finely grind the outer surface of the shaft to ensure the flatness and accuracy of the shaft surface.
Surface finishing is a process that uses mechanical grinding methods to remove surface unevenness and roughness by cutting or rubbing the workpiece surface, thereby improving surface quality and precision. The outer edge grinder is a special grinding equipment, mainly used for precision grinding and processing of the outer edge of the workpiece.
The following effects can be achieved by fine grinding of the surface using an external edge grinder:
- Improve surface accuracy: The outer edge grinder can accurately control the position and movement trajectory of the grinding wheel, realize precision machining of the workpiece surface, and improve surface flatness and accuracy.
- Improved surface quality: The high-speed rotating grinding wheel of the peripheral grinder cuts and rubs the workpiece surface, which can effectively remove surface defects, oxide layers, and roughness and improve surface quality.
- Enhance workpiece wear resistance: The surface of the workpiece after fine grinding by the outer edge grinder is smoother and flatter, which can improve the surface hardness and wear resistance and extend the service life of the workpiece.
Dimensional inspection passed:
The shaft dimensions are strictly measured and inspected to ensure that the shaft meets the design size and tolerance standards.
Finished shaft:
After the above process, the final finished shaft is obtained. The above process includes the whole process from raw materials to the final finished product, ensuring that the quality and performance of the supporting wheel pin meet the design requirements.
Advantages of track roller pins:
High precision: After rough turning, fine machining, and dimensional inspection, the shaft is ensured to have high dimensional accuracy and meet the design requirements.
High-quality surface: After heat treatment and surface grinding, the shaft surface is flat and smooth, which improves the wear resistance and surface hardness of the shaft.
Good durability: Surface tempering treatment is carried out through heat treatment to improve the hardness and wear resistance of the shaft and extend the service life of the shaft.
UT flaw detection ensures that there are no defects such as cracks inside the shaft, which increases the safety of shaft use.
Environmental friendly: Rationally utilize raw materials, reduce waste generation, and meet environmental protection requirements.
In general, the track roller pin machining process is carefully designed and strictly controlled, with the advantages of high precision, high-quality surface, good durability, safety and high efficiency, and is suitable for applications in mechanical transmission systems and other fields with high requirements.
2. Wheel Body
The roller body of the rotary drilling rig plays an important role in the entire roller structure. By supporting and bearing weight, transmitting power, increasing inertia, and protecting other components, it ensures that the roller plays its due role in the operation of the rotary drilling rig and guarantees the normal operation and safety of the drilling rig.
Mold manufacturing:
The mold is a key tool for producing the wheel body of the track roller. The quality of the mold directly affects the forming quality and dimensional accuracy of the product. During the mold manufacturing process, the mold needs to be made according to the product design requirements and ensure that the mold size is accurate and the structure is reasonable. After strict inspection, qualified molds can be put into use, and unqualified molds need to be repaired or replaced.
Cutting:
Cut the raw materials according to the design requirements.
forging:
The forging process is used to shape the raw materials to ensure that the dimensions meet the requirements.
Rough turning:
The forged wheel body is rough-processed to remove excess material and preliminarily shape the wheel body.
Heat Treatment:
The heat treatment of the roller body mainly includes quenching tempering and medium frequency. Quenching and tempering and medium-frequency induction heating are two commonly used heat treatment processes, which play an important role in the processing and modification of metal materials. The processing effects of quenching and tempering and medium frequency induction heating on the roller body mainly include the following aspects:
Improve material hardness and strength: Through tempering treatment, the organizational structure of the supporting wheel body can be improved, so that it can increase its hardness and strength while maintaining a certain toughness, enhance its compression resistance, wear resistance, and deformation resistance, and improve its service life and durability.
Improved processing performance: The quenching and tempering treatment can eliminate the residual stress and structural defects generated in the wheel body of the supporting wheel during the processing, improve its processing performance, and facilitate subsequent mechanical processing and surface treatment.
Improve wear resistance: After tempering treatment and medium frequency induction heating, the surface hardness of the track roller body is improved, thereby improving its wear resistance, extending its service life and reducing failures caused by wear.
Improve heat treatment uniformity: Medium frequency induction heating can make the roller body heated evenly during the heating process, avoid local overheating or overcooling, and improve the overall heat treatment effect and performance stability.
Welding
The wheel body welding adopts a fully automatic welding process, which is a process that uses automated equipment and systems to complete the entire welding process. The necessary welding process is carried out to ensure the structural integrity of the wheel body.
The fully automatic welding system can realize the automatic movement and welding of the welding gun or welding wire according to the preset welding path and parameters, thereby completing the welding process. The fully automatic welding system is usually equipped with an online weld detection and quality feedback system, which can monitor the welding quality in real-time and adjust the welding parameters in time to ensure that the welding quality meets the requirements.
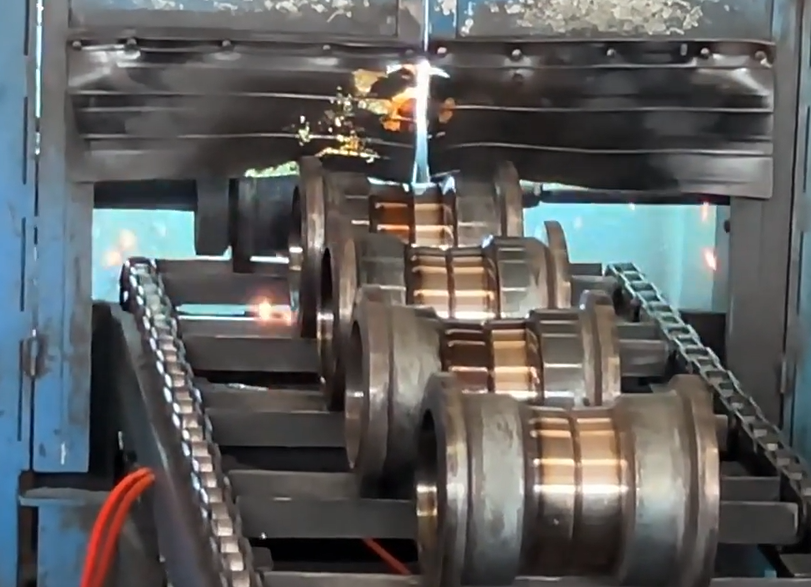
UT (Ultrasonic Testing) Inspection:
UT (Ultrasonic Testing) is a non-destructive testing technology, which is often used to detect internal defects, cracks, pores and other problems in materials. Ultrasonic testing technology is used to detect whether there are defects in the weld.
UT testing has the advantages of high sensitivity, high resolution, and strong quantitative capability. It can detect tiny defects and provide detailed defect information.
Finishing:
The assembly process of the guide wheel Video
The wheel body is precisely processed using CNC machine tools and other equipment, including turning, milling, hole processing and other operations, to improve the accuracy and surface quality of the wheel body.
Pressed copper tile:
The bearing is the matching part between the track wheel and the shaft.Steel Alloy, used to support and fix the position of the shaft, reduce the friction and wear between the shaft and the supporting wheel, and ensure the normal operation of the shaft. The wheel body is treated with copper alloy material to increase wear resistance.
Test:
Carry out a comprehensive inspection on the finished track roller body to ensure that it meets the design requirements.
Wheel assembly
The wheel bodies that have passed the inspection are assembled into the final supporting wheel product.
Advantages of track roller body:
Material selection: The wheel body of the track roller is made of 40Mn2/50Mn round steel. Both materials are medium carbon alloy steels with high strength and hardness and are suitable for making mechanical parts that need to withstand large loads and vibrations.
During the forging process, 40Mn2 and 50Mn can achieve the ideal forming effect by controlling the temperature and pressure, ensuring the dimensional accuracy and uniformity of the internal structure of the roller body. After the forged roller body is subjected to heat treatment and other processes, it can obtain the appropriate hardness and strength to meet the use requirements.
Process advantages: The use of round steel forging for the track roller can increase its density and strength, because the forging process can rearrange the grains inside the metal, thereby improving the strength and hardness of the material. In addition, the overall durability of the track roller can be further improved by quenching and tempering (WSQ hot quenching process), increasing its wear resistance and impact resistance.
quality assurance: The fully automatic welding process can ensure the quality and consistency of the welds, while the weld flaw detection quality inspection is used to detect whether there are defects or cracks in the welds to ensure that the welding quality meets the requirements and improve the safety and reliability of the supporting wheels.
3. Other parts
End caps
It mainly plays the role of dustproof and sealing during the working process of the supporting wheel, preventing dust from entering the wheel body and causing damage. The bolts and nuts fix the entire supporting wheel on the frame through the bolt holes at both ends, thereby playing the role of axial positioning of the outer ring of the supporting wheel.
Process: Ductile iron (spheroidal graphite is obtained through spheroidization and treatment, which effectively improves the plasticity and toughness of cast iron).
Floating oil seal, “o” ring
Floating oil seal, “o” ring: A seal, a compact mechanical seal developed to adapt to harsh working environments. It has the advantages of strong anti-pollution ability, wear resistance, impact resistance, reliable operation, automatic compensation for end face wear, simple structure, etc. It is most commonly used in engineering machinery products.
Principle structure: The floating oil seal is composed of two identical metal rings and two “0”-shaped rings. Its working principle is that a pair of rubber rings form a closed space with the cavity under the support of the metal rings. When rotating, the two ground surfaces of the metal rings (there is a bulge in the middle of the metal between the two floating oil seals, and the two bulge lines are in contact) fit closely and slide relative to each other, which on the one hand ensures good operation, and on the other hand effectively seals off external dust, water, sludge, etc., and protects the internal lubricating grease from leakage.
Sealing principle:The two floating rings rely on the deformation of the “O” ring after axial compression to generate a pressing force on the sealing end face of the floating ring. As the sealing end face wears evenly, the elastic energy stored in the “O” ring is gradually released, thus playing an axial compensation role.
Advantages of Track Roller Products
Track rollers play an important role in engineering and mechanical equipment. They are usually used to provide additional stability and support to ensure the balance and safety of the machine when it is working. By optimizing the manufacturing process of track rollers, their quality and performance can be improved, making them more superior. Our track roller products have the following advantages:
Premium materials and workmanship: Using round steel forging and tempering and surface quenching technology, the track roller products have higher density, strength, and durability, can withstand greater loads, and have a longer service life.
Stability and Security: The fully automatic welding process and weld flaw detection quality inspection ensure welding quality and consistency, reduce the possibility of welding defects, and thus improve the stability and safety of the supporting wheels during work.
Superior performance: The optimized process of the track roller can improve its wear resistance and impact resistance so that it can still maintain good performance in harsh working environments and be more durable and reliable.
Stable and efficient: The use of fully automatic welding processes and modern production technology can improve the production efficiency and consistency of supporting wheels, reduce waiting time for stocking, and reduce downtime and maintenance losses.
For expert rotary drilling rig undercarriage parts services and supler, contact Yantai Orient today!