1. Uneven or Scalloping Wear of Track Link
Scalloping wear of track link is normal for high speed machines with high mileage.
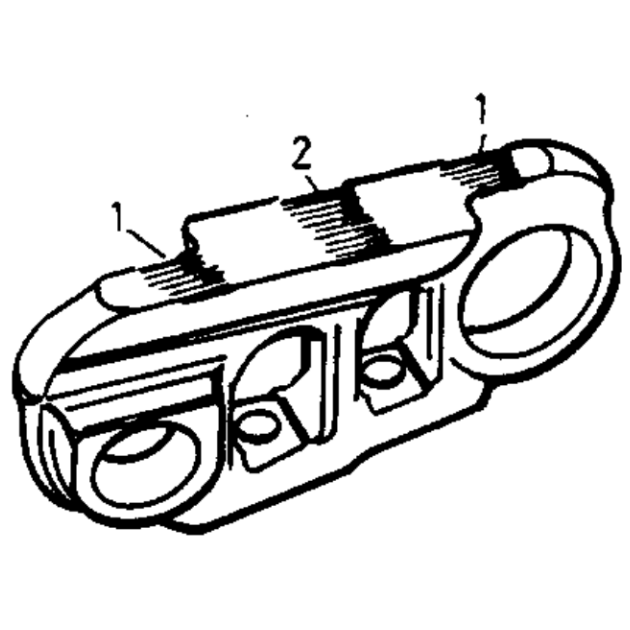
- Causes
End scallops (areas #1) are caused by the reduced surface area where the links overlap, this situation increases specific pressure and thus the wear rate.
Pitch extension due to internal wear of the joint increases this effect.
Center wear (#2) is due to the reduced contact area between the link flat surface and the curved idler tread.
- Accelerators
Speed, weight, horsepower, impact, abrasiveness, shoe width, track tension.
Machines equipped with two idlers instead of one display faster wear.
- Effects
Premature wear in the area above the pin boss reduces wear life of chain.
Machine vibrates and moves from side to side during transportation.
- Remedies
Equip the machine with a sealed and lubricated track (SALT) chain (if not already present).
Maintain proper track tension.
2. Rail Side Wear of Track Link
Heavy wear at transition from link top to link side.
Can be found inside and/or outside the link.
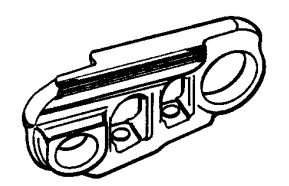
- Causes
Contact of the links against roller and idler flanges.
This situation can also be caused by fitting a new track chain on an undercarriage with heavily worn rollers. In this case the wear pattern of the rollers is transferred onto the track links ( bow type wear ).
Misalignment of one or more components of the undercarriage. Track chain is
forced in line by roller flanges.
- Accelerators
Same as “Uneven or Scalloping Wear” plus turning speed, extremely large track shoes when operating on high impact terrains.
- Effects
Reduced wear life because of increased specific pressure.
New rollers wear faster if installed and operated with a worn track chain.
- Remedies
Replace all undercarriage components at the same time.
Reduce controllable variables as far as possible by using narrower track shoes alternating work directions on sidehills and checking U/C alignment.
Also snaky track chains should be replaced.
3. Rail Inside Gouging
Wear on internal side of the link concentrated on one or more points at regular intervals.
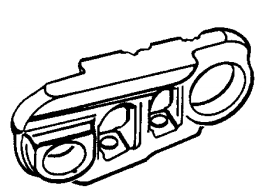
- Causes
Interference between the link and sprocket tooth tips, due to:
- Misalignments between track and sprocket;
- Snaky chain during steering actions;
- Use of incorrect sprocket.
- Accelerators
Sidehill operations with wide track shoes
- Effects
Reduced reusability of links and sprockets
- Remedies
Eliminate misalignments and use shoes with the proper width.
Use track guides.
Use the proper sprockets.
4. Elongation of the Counterbore
Extension or ovalization of the bushing counterbore
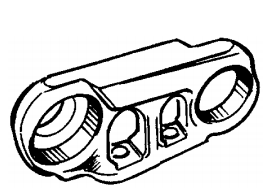
- Causes
Rotation of the bushing in the link as a direct result of a pitch extension.
This can also be due to a seal failure that will result in internal seizure.
- Accelerators
Wide track shoes.
- Effects
Reduced re-usage of the links, even with new seals.
- Remedies
Turn pins and bushings at the service limits.
Avoid sudden speed variations.
5. Pin Boss Wear of Track Link
Wear on the bottom side of the link pin boss
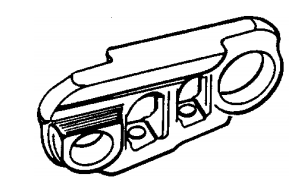
- Causes
Contact between the pin boss with the top of the roller flange due to the fact that the wear life of the roller treads and link wear surface has been exceeded.
- Accelerators
Concentrated and uneven loads on the first rollers (front or rear) of the undercarriage, for causes attributable to the application.
- Effects
Reduced pin retention resulting in possible machine downtime and further damage to other undercarriage components.
Re-usability of links with pin and bushing turn or rotation (servicing) and chain rebuilds are precluded.
Vibration in high-speed applications.
- Remedies
Monitor wear of undercarriage components and service/replace worn-out parts in good time.
Compensate for high loads on front or rear of machine by using counterweights.
6. Rail Spalling
Chips detaching from side of the link rail.
The link should be considered affected by this problem only if the total length of spalling is longer than 30% of the total length of the link. Otherwise, the damage can be classified as purely superficial (and/or “cosmetic”).
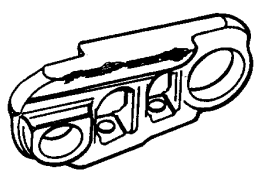
- Causes
Normally caused by heavy impacts between the link and the roller treads and flanges.
This could also be caused by fitting a new chain on an undercarriage equipped with worn rollers. In fact, the high specific pressure due to the very small contact area work hardens the surface of the link corners. At the same time, it generates micro cracks below the surface at the level of the maximum stress concentration. These cracks propagate and will result in detachment of a chip of steel in a relatively short period of time.
- Accelerators
Excessive track tension, wide shoes, impact, machine speed and weight.
- Effects
Reduced wear life; re-usability.
- Remedies
Avoid installing new track chains on rollers with heavily worn treads.
Reduce or eliminate the effects of controllable variables like shoe width and track tension.