To prevent damage or wear to other track assembly components such as track chains, it is crucial to promptly replace track roller in case of oil leakage or bearing seizing. When the track roller fails to rotate, increased friction between the bottom roller housing and the track accelerates track wear. Simultaneously, the hydraulic system driving the track units detects increased pressure due to the greater power required for track propulsion. This places additional stress on other mechanical components, such as the gear faces of the sprocket or the bushings protecting the track pins.
Bottom roller replacement is typically prompted by bottom roller oil leakage. However, it’s essential to differentiate between actual oil leakage and minor seepage. A small amount of oil leakage from sliding bearing seals is entirely normal and referred to as “weeping” in professional terms. This is common with sliding bearing seals, where the leaked grease cleans the sliding surface and prevents debris from entering the bottom roller’s roller bearings or sliding bearings.
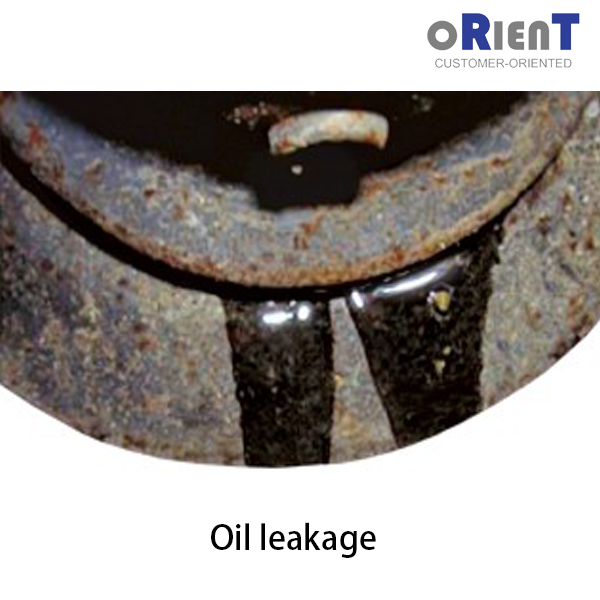
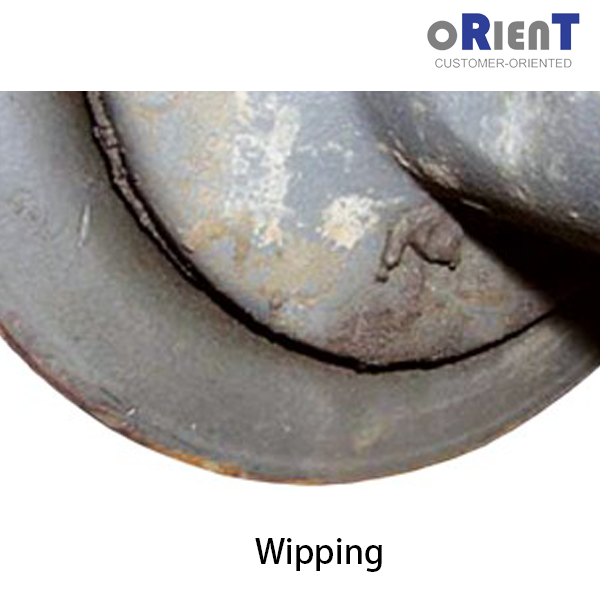
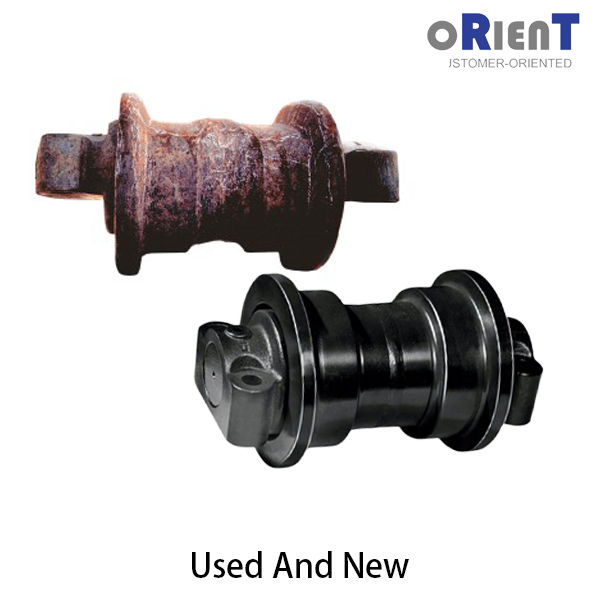
Common Causes of Damaged Track Bottom Rollers:
Uneven loads lead to premature damage. Failure to replace bottom rollers as a set during maintenance results in uneven wear and uneven load distribution.
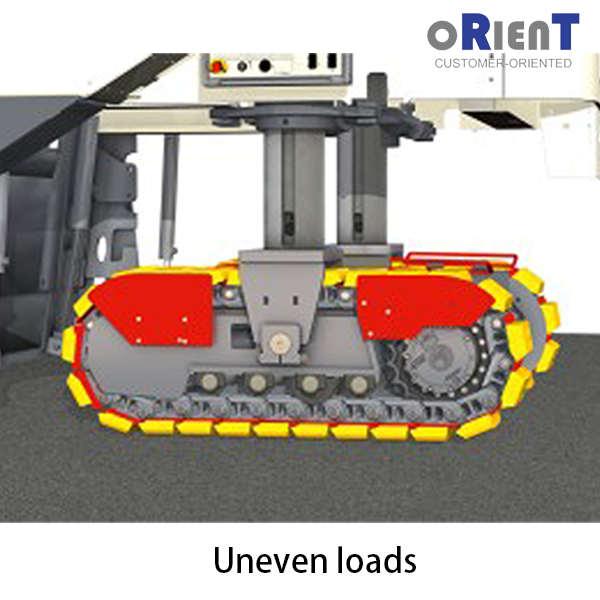
Repeatedly running over curbs causes imbalanced loading on the bottom rollers. Additionally, insufficient reduction in the diameter of the bottom rollers to support vertical pressure results in excessive loading on the wheel bearings and the gearbox of the sprocket.

If you have any inquiries about Drilling Rig Undercarriage Parts, such as track shoes, track chain assembly, track roller, carrier roller, sprocket, and idler. Please feel free to contact us.
Our Alibaba: https://ytrtzg.en.alibaba.com/?spm=a2700.shop_cp.88.12