Rotary drilling rigs can tip over due to an imbalance in their center of gravity. It caused severe damage to the rig’s engine, structure, hydraulic components, and other parts. This could even lead to injuries or fatalities.
Tipping Causes
The rig’s large weight and the high pressure of the track on the ground can raise the center of gravity, leading to tipping.
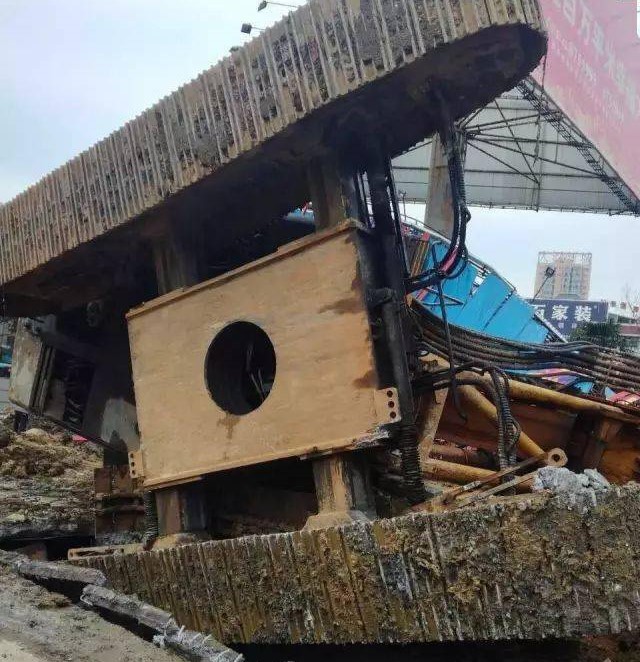
Tipping Types
Hole Collapse Tipping: This can occur if the correct technology isn’t selected based on hydrological and geological conditions. Factors like a short casing and poor slurry quality can cause the casing around the hole to collapse, leading to potential tipping.
Hidden Mud Pool Tipping. Abandoned mud pools at construction sites, if not cleaned and backfilled, can trap the rig, causing it to tip over.
Pile Head Tipping. Unbackfilled pile heads at construction sites can also cause the rig to tip over if the front side of the rig’s track presses on them.
Riverbank Soft Tipping. The rig can tip over if it’s driven to a location softened by river water.
Pressure Collapse Hole Tipping. The track can collapse the nearby pile hole if a hole is made dry, causing the rig to tip over.
Backfilled Soil Tipping. Loose backfilled soil can cause the rig to tip over if the drill rod is lifted high, causing the center of gravity to move forward.
Access Road Tipping: The rig can tip over if it’s forced through a soft road section.
Hanging Drill Rod Tipping: The rig can tip over if the mast leans forward at a large angle.
Flat Car Tipping: The rig can tip over if it doesn’t control the center of gravity well.
Tipping Prevention
Adjust the Center of Gravity: Adjust the center of gravity of the whole machine continuously based on real-time road conditions.
Lower the Mast/Shrink the Track. Lower the entire mast to reduce the center of gravity of the whole machine in dangerous road conditions.
Pad Steel Plate. Lay steel plates to increase the contact area, reduce the track ground pressure, and reduce the probability of tipping.
Construction Technology. Determine the construction technology according to the hydrology and geology.
Monitoring. Monitor various aspects during drilling to prevent hole collapse and tipping.
Warning Bar/Mark. Use a warning bar or marking method to warn of danger after backfilling the mud pool.
Backfill Empty Pile Head. Backfill empty pile heads to avoid being pressed by the drilling rig and eliminate hidden dangers.
Exploratory Walking Machine. Use the drill rod drill head to touch the ground and probe the road conditions if they can’t be determined.
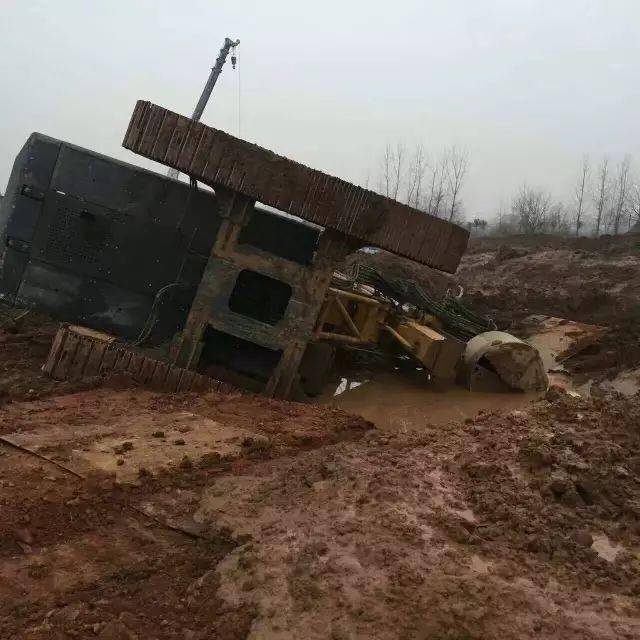
Tipping Solution
Increase Counterweight. Use the drilling rig/excavator to press the drilling rig and increase the counterweight effect to prevent or alleviate the drilling rig from tipping.
Excavator Support. Use the excavator to support the drilling rig mast to prevent tipping.
Lifting the Drilling Rig. Use two cranes to lift the rotary drilling rig upright if it’s seriously tilted or has tipped over.
If you have any inquiries about Drilling Rig Undercarriage Parts, such as track shoes, track chain assembly, track roller, carrier roller, sprocket, and idler. Please feel free to contact us.
Our Alibaba: https://ytrtzg.en.alibaba.com/?spm=a2700.shop_cp.88.12