Track pads are subjected to heat treatment to improve their hardness, strength, and wear resistance, thus increasing their service life. This is typically achieved through methods like tempering and induction hardening.
Heat treatment plays a crucial role in enhancing the mechanical properties and overall performance of metal components. Here are some key reasons why heat treatment is important:
Improving mechanical properties: Heat treatment can significantly alter the microstructure of metals, resulting in improved mechanical properties such as hardness, strength, toughness, and ductility. This enables the material to withstand various types of mechanical stresses and loads more effectively.
Enhancing wear resistance: Heat treatment techniques like surface hardening can increase the hardness and wear resistance of metal surfaces, making them more resistant to abrasion, erosion, and frictional wear. This is particularly important for components subjected to high levels of wear and tear in industrial applications.
Increasing dimensional stability: Heat treatment can help relieve internal stresses within metal components, reducing the risk of distortion, warping, or cracking during subsequent machining or use. This ensures better dimensional stability and tighter tolerances, leading to improved part quality and performance.
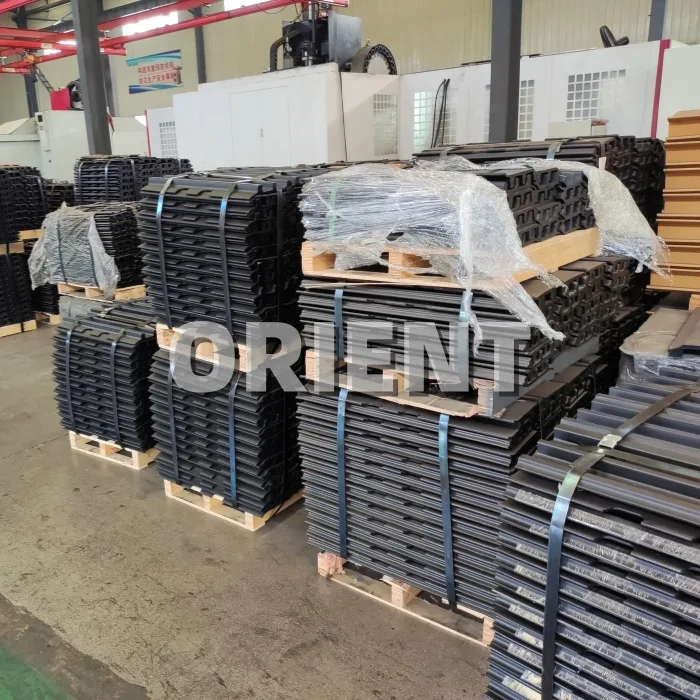
What are the advantages of heat-treated track plates?
Enhanced hardness and strength: Tempering during heat treatment improves the hardness and strength of track pads by controlling the material’s structure and properties, thereby enhancing their compressive, tensile, and impact resistance.
Improved wear resistance: Heat treatment increases the surface hardness of track pads, improving their wear resistance and prolonging their service life, thus reducing replacement frequency and maintenance costs.
Increased impact toughness: Tempering improves the impact toughness of track pads, enhancing their resistance to impacts and reducing the risk of fractures and damage caused by collisions or external forces during use.
Maintained good machinability: Induction hardening ensures a uniform and stable internal structure of track pads, reducing the occurrence of cracks and deformations and maintaining good machinability for subsequent processing and shaping.
Enhanced product quality and reliability: The combination of tempering and induction hardening ensures the consistency and stability of track pads, improving product quality and reliability while reducing quality fluctuations and failure rates during production.
Energy and cost savings: Induction hardening offers advantages such as high energy utilization efficiency and rapid heating compared to traditional heating methods, leading to energy and cost savings, increased production efficiency, and economic benefits.
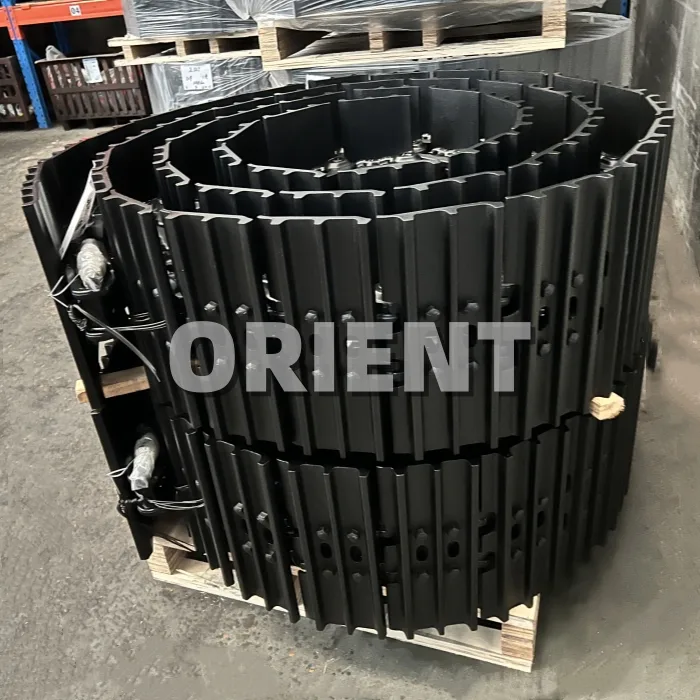
If you have any inquiries of undercarriage parts, please feel free to contact us.
- Email: info@heavyindustryparts.com
- Alibaba: https://ytrtzg.en.alibaba.com/?spm=a2700.shop_cp.88.12